We’ve been awfully excited to use 100% recycled plastic for the shells of our robotic construction kit. We were going to end up using two materials for the blocks: black recycled ABS and clear recycled PET (from soda bottles). Using materials that have already been around the block and into the bin made us feel better about our contribution to the mountain of stuff around us. And that’s why it’s pretty upsetting to find out that we probably cannot use recycled plastic at all.
In 2008, the Consumer Product Safety Improvement Act (CPSIA) was signed into law in the US. Don’t get us wrong, the law is a good thing: it protects kids from lead and other harmful substances in toys, and requires mandatory third party testing for all children’s products. One important group of substances regulated by the new law is phthalates, which are chemicals added to plastic during manufacturing to make them more flexible and durable. Heavy exposure to phthalates, unfortunately, has been shown to cause endocrine disruption and infertility.
To comply with the CPSIA, our plastic must meet a certain requirement for phthalate levels. But since recycled plastics are just a mix of old plastics ground up and reheated, no supplier will guarantee that every part will meet the requirements. So while we haven’t given up on our search for a better option, unfortunately it looks like our only option is to use virgin plastic. Any thoughts?
Category: Uncategorized
A tip of the hat to Pittsburgh’s Kids & Creativity group – a loosely linked collection of artists, media folk, museum directors, hackers, teachers, professors, businesses, philanthropists, all working to make the Pittsburgh region an amazing place to be a kid. And because Pittsburgh is a center for both technology and the arts, many of the projects work at this intersection. The group — now about a hundred strong — meets monthly for a vibrant exchange of information and ideas, and yesterday’s meeting at the Carnegie Science Center was a flood of conference and meeting reports, from the Game Developers to Interaction Design for Children to SIGGRAPH. I’m relatively new to Pittsburgh (5 years now) and through Kids and Creativity I get to hang out with the most amazing and committed and imaginative people. Kudos to Gregg Behr, executive director of the Grable Foundation, who seems to know everyone and has that special knack to bring very disparate worlds together.
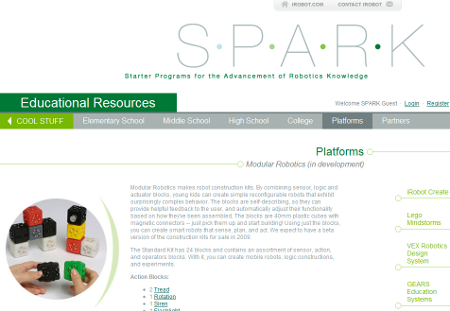
3D printers are amazing tools: design an object on your computer, hit control-P, and when you come back from lunch, a nice warm plastic part is waiting for you. For a few years now, I’ve been making prototype plastic parts on a trusty Stratasys Dimension. It’s quick and makes robust ABS parts at the touch of a button: I just draw in Solidworks and usually have a finished part the next day. But at the scale of parts for the robotic construction kit that we’re working on, we’ve run up against a resolution wall. The Dimension, with a resolution of about 178 microns, just can’t print print the fine details I need at this stage of design.
Enter the Objet Eden. It’s different technology; the material is deposited by a bunch of print heads in parallel, much more like an inkjet printer than the “hot glue gun on a robot” style of FDM. And the parts are beautiful. Layers are only 16 microns (16 microns!) thick, so parts are smooth to the touch, even shiny, when they come out. The picture above is a test print of a 40mm cube, and it’s perfectly smooth; no ridges or bumps. It’s fast, too — these parts printed in 80 minutes. The material seems strong and durable, and the support material washes off with water. The only catch is that the machine costs about $115,000.
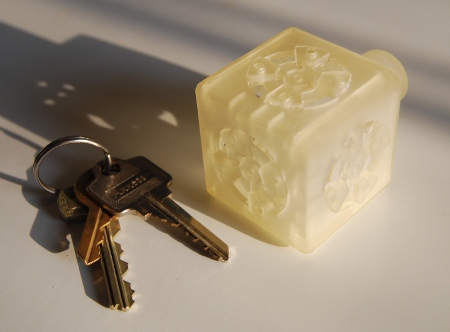
I wanted to pick up a 12VDC charger for my fancy new iPhone. I peeked at Apple.com first and found one for $19.95 (plus $4 shipping). Electronics stores like Best Buy had similar offerings. Twenty plus dollars to plug my phone into a cigarette lighter seemed a little expensive especially since I happen to have a bunch of voltage regulators lying around my desk at any given point. I saw that Sparkfun had an iPod plug for $5, but I had already tried my phone with my iPod charger and it didn’t work. Current? Pins? Who knows. Then I did a quick search on eBay.
I was skeptical. $0.99 for a charger with free shipping? But the seller had 1,377,576 feedbacks with a 99.7% success rate. Anyway, what did I have to lose; ninety-nine cents? But two days later the charger you see above arrived at my door and I’m pleased to report that it works swimmingly.
Truthfully, though, I don’t understand how this can happen. I’m currently spending a lot of time and energy trying to reduce the cost of our robots, and while I can imagine being able to make this charger so that it sells for $0.99, I have no idea how they can ship it to me (from CA to NY!) for free. It began its journey with DHL and then was transferred to the US Postal Service, so I’m not even sure where it originated from. Shenzhen?
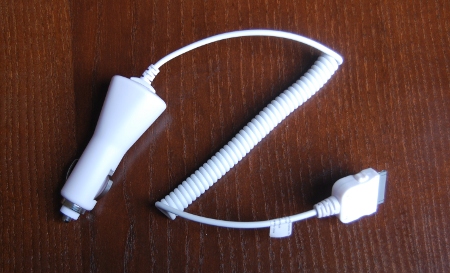
We changed our name to Modular Robotics and we have this fantastic new logo. I think it would make a really good sticker. Or maybe we’ll give away stencils for it and cans of baby blue spray paint. We haven’t settled on the new name for the kit yet, but we’re getting there. Instead of roblocks.org, find us at www.modrobotics.com.
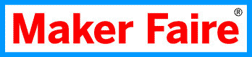
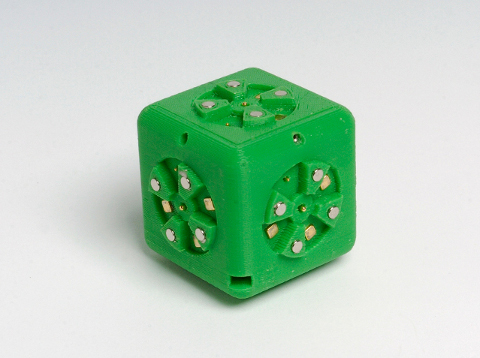
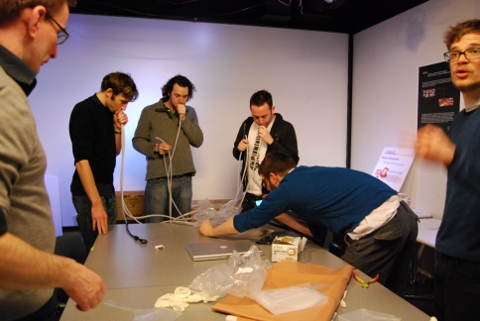
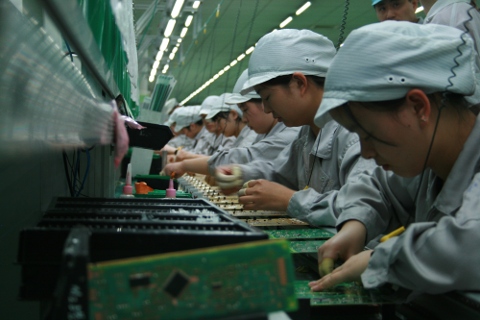